Service
Maximum uptime guaranteed with our ongoing support
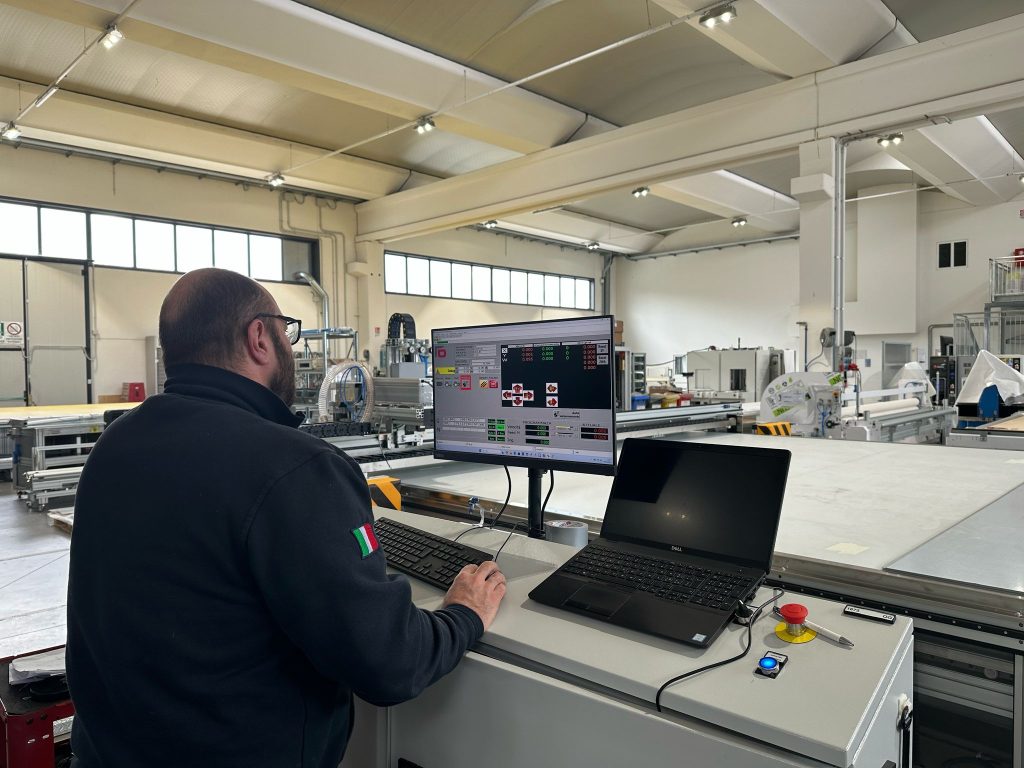
Continuous and reliable support
Cutting Edge Automation Machine Service Department counts on the contribution of a structured team within technicians, back office and remote assistance specialists.
We know that machine downtimes lead to productivity losses, that’s why our main target is to guarantee our customers a quick and expert service.
We can manage assistance from remote or at customer’s site, depending on the specific need, and our service offer aims to meet each customer’s needs.
For any request please fill the form on the page.
Our service solutions
Machines Installations
Our product experts will install your new machine rapidly and efficiently. The installation includes: mechanical and electrical installation, commissioning, initial setup, training on safety features and on all functionalities of the machine.
Remote Assistance
Our back-office technicians will manage your request in few days and, if necessary, will arrange a technical intervention at customer’s premise.
Training
Cutting Edge Automation Machines Service Dept. organize trainings, if required, in different locations, according to customers needs. The training will be customized on operators knowledge and skills.
Customized solutions
We provide customized solutions as we consider our customers “unique” and we are proud to offer dedicated services that support our partners in reaching the desired production efficiency.
Scheduled periodic maintenance
Annual maintenance planning should be scheduled to avoid production failures before they occur, reducing risks of emergencies.
Spare parts and tools
We can provide a kit that includes spare parts and tools based on production forecast and machine usage.
Discounted service agreement rates
By securing our preventive maintenance package, you are entitled to discounted rates on maintenance, on special maintenance and on spare parts.
Qualified consulting and training
Our experts will guide and train you on the correct usage of your machine and how to improve production processes. They will also keep you updated regarding any new accessory that might become available, including installation updates to your machines. We can even offer periodic training sessions for your staff.
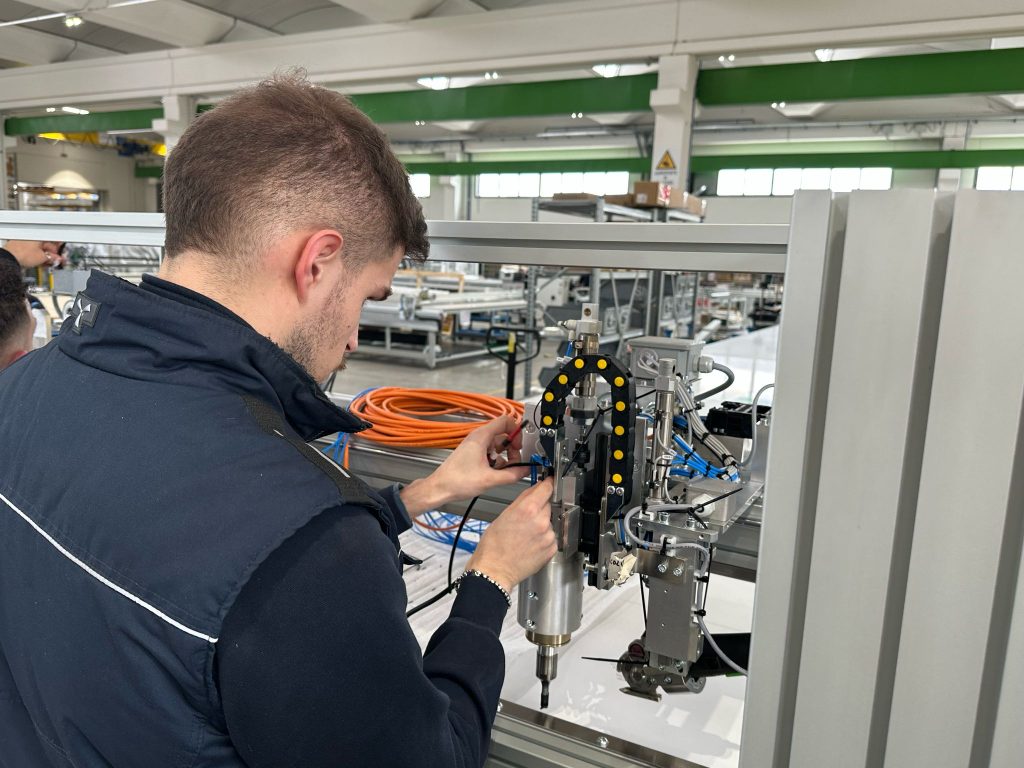
The advantages of preventive maintenance
With effective maintenance planning, you can increase your production efficiency from +5% to +10% and obtain an average waste reduction from 5% to 15%.
By signing up for a preventive maintenance plan, you will generate value in terms of productivity and production efficiency, which will mean a return on investment over time.
Preventive Maintenance Advantages:
• Reduced downtimes
• Spare parts always available
• Maintenance can be scheduled according to the production plan over the year
• Low and predictable maintenance costs
Contact our service
Fill out the form and you will be contacted quickly
Write also on Whatsapp
+39 345 15 33 446
Why choose us?